Firestopping in the Commercial Construction Industry
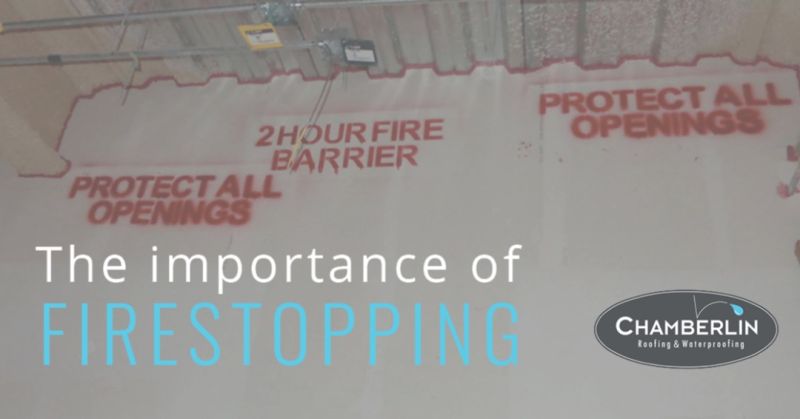
Firestopping is an integral component of a fire prevention plan during building construction intended to help restrict the spread of fire by containing it within a room or area of the building. The room typically will have fire-rated walls, ceiling and floor. Many walls and/or floors contain openings for mechanical, electrical, plumbing and sprinkler (MEPS) penetrations to allow pipes, ducts and cables to pass through. Firestopping materials are used to limit fire spread through penetrations in a fire barrier. Hilti Market Development Manager Stefan Juli says membrane penetrations are problematic because “if you have a fire, and smoke gets in a chase wall, smoke can easily go upward and actually spread through the building.”
The idea of compartmentation came about from the shipbuilding industry. Once boats, particularly warships, began to have different compartments connected with ventilation and cables, compartmentation became more necessary, especially considering the wooden structures.
What to Know
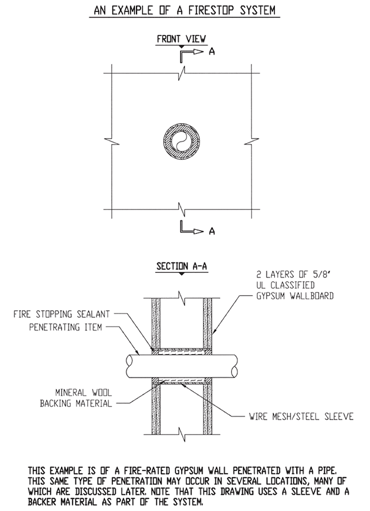
“It’s not uncommon to see a fire barrier penetrated during a minor building alteration, and then the penetrating
item isn't protected by firestopping,” says Chris Jelenewicz, technical director of Society of Fire Protection Engineers (SFPE). Many MEPS and other trade contractors’ services can leave holes in the barriers, some of which can be difficult to detect. If the penetration isn’t properly sealed and protected with an appropriate firestop system, the fire barrier is rendered less effective, and fire will spread beyond the compartment of origin.
Knowledge of proper material to use and proper installation techniques are vital to the system being effective. Chamberlin’s years of extensive expertise and hands-on experience have taught us a thing or two.
Factors for consideration:
- Code and testing system requirements and ratings (F, T, L, W)
- Tolerances – annular space sizes, angles
- Gap Sizes – undercuts, framing
- Anchors – spacing, hardware
- Inspections and maintenance
Not only will you benefit from our know-how, but we can be a one-stop shop for your waterproofing scopes. While many waterproofing contractors do not include firestopping installation in their scope of services, Chamberlin Roofing & Waterproofing can complete it all with a single point of contact for your project. "Our ability to provide high-quality firestopping within our waterproofing scopes can be a real asset to a contruction management firm and building owners. Chamberlin knows what they are doing and how to do it properly," says Chamberlin Vice President l General Manager Andy Wharton.
Tell Me More…
What are referred to as basic fire suppression systems, such as sprinklers and fire extinguishers, are probably more familiar to most people than passive fire protection. Passive fire protection (PFP) systems refer to the elements of a fire protection system such as fire-resistant structural components, compartmentation and firestopping materials that contain the fire at its point of origin. Building owners and property management professionals should be aware of the codes and ratings associated with each PFP system in the building and also consider what an important part maintenance plays in these systems working properly over time.
“Building owners and facility managers are important stakeholders in a building’s fire protection program,” says Jelenewicz. “As such, they should play an important part in every phase of building modification to ensure that life safety is not impacted," he continues. "This includes the planning, design, construction and maintenance of the building.” If renovations have been made to a building, or part of a building, such as new electrical wiring or plumbing, there is the chance that penetrations have been made in fire barriers.
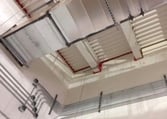
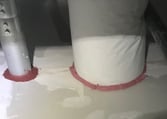
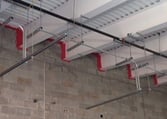
.John Sinisi, Sinisi Associates LLC owner, recommends beginning an assessment of your facilities’ firestop with the following questions:
- Where are there rated walls and floors in your building?
- Are the penetrations and tops of walls sealed?
- If sealed, what tested system design was used for the repair?
- Does the repair match the tested system design detail?
It is important to note that most professionals recommend redundancy in fire protection. In other words, a fire-sprinkler system, alarm systems and occupant education in conjunction with passive fire protection systems are a safer, more balanced approach to protecting your building and the people inside.
History
As mentioned above, the idea of firestopping came about in the shipbuilding industry. Then came the fire at Browns Ferry Nuclear Power Plant in Alabama in the mid-70s, which is reported to have brought the concept to land. The plant was being inspected for air gaps, which could potentially allow for the leakage of radioactive material. The typical testing method at the time was holding a lit candle to see if air movement would cause the candle's flame to flicker. During one such test, the flame came close enough to polyurethane foam that was used to block air movement around cables. Despite having a flame retardant applied, this foam was still flammable and ignited a fire through the wall.
Even more notable in the progression of fire protection was the MGM Grand Hotel fire in Las Vegas in late 1980. The fire that surged through the twenty-six-floor hotel with 2,078 rooms left over six hundred people injured and 85 dead. The air handling system, elevator shafts, openings in vertical shafts, seismic joints, fire stairs, electrical and plumbing systems, and even some broken windows on the windward side of the building all worked as activators to spread smoke and heat all the way through the 26th floor.
The hotel's high-rise tower evacuation alarm system was destroyed before fire alarms could activate. The design and operation of the hotel violated codes and practices for smoke control. Among other synthetics, the hotel had PVC drainage pipes between the casino ceiling and the floor of the first story as well as a vast electrical network insulated in PVC plastic. Wall coverings, rigid molded furniture and fake leather upholstery also contained PVC. The issue with PVC is that it quickly decomposes and, when combined with other synthetic polymers found in the casino, emitted dangerous chemical agents.
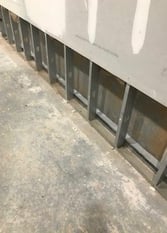
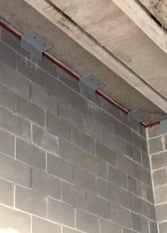
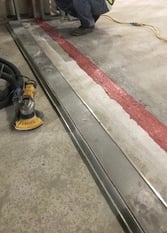
The fire started at 7:30 am in the casino deli electrical system and quickly ignited the synthetic materials, due to flashover and lack of fire-resistant barriers. Large amounts of air flowing through the adjacent coffee house and arcade provided a fresh air supply for the fire. The flames spread the length of the 200-yard casino in under six minutes at a burning rate of over 15 feet per second. The hotel had partial sprinklers but major areas including the casino and the deli did not have a fire sprinkler system installed. What was unusual about this fire was the fact that the majority of the fatalities occurred from smoke inhalation on the 19th through 26th floors, far from the fire. Large quantities of smoke rose to the top of the building, accumulated, sunk down and then rose again. Control over the fan system was lost when its PVC tubing melted in the early stages of the fire, so the fans continued to push smoke around the building
The MGM Grand fire underlined the importance of fire prevention, and later newspaper articles indicated that there were 83 building code violations, design flaws, installation errors and materials that were identified afterward that contributed to the magnitude of the fire and smoke spread. In the face of the possibility of similar tragic events in the future, it was decided to focus on improving fire prevention and life safety. This not only was the case in Las Vegas but soon catching attention throughout the industry.
As the industry developed, standards were created to ensure that various manufacturers' materials all conformed to the same requirements. The firestop industry was written into the building code in the 1980s. These new requirements were often misunderstood and seen as an unnecessary expense causing corners to be cut and inadequate materials to be substituted that were not proven firestopping products. As time went on, more contractors learned the importance of the new standards and more building officials learned how to identify the difference between red drywall mud, red latex caulking and actual firestop material.
According to James C. Shriver, director of technical services at Thermafiber Inc., "A part of what we have learned from these fires is that the construction systems we specify today have an important role to play in the safety of buildings and their occupants many years from now."
SOURCES
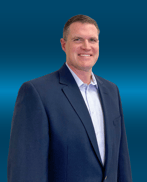
Andy Wharton, Chamberlin Vice President l General Manager - Waterproofing and Caulking, North Texas and Oklahoma. Andy graduated from Texas A&M University in College Station, Texas, with a Bachelor of Science in Environmental Design. He has over 15 years of experience working with commercial and industrial properties developing waterproofing solutions to keep water out of their assets. In his position at Chamberlin, he manages new and remedial construction waterproofing jobs, overseeing an office and field operations team. Some significant projects he has been involved with at Chamberlin include Dallas Cowboys Headquarters and The Ford Center at The Star in Frisco, Texas, which was awarded a 2017 TEXO Distinguished Building Award. He is an active member of the A/E/C industry participating in the American Subcontractors Association, TEXO and Firestop Contractors International Association. Additionally, he is involved with Kistruction, Kidsbuild, Pink Heals of Colin County.
Buildings magazine “The Basics of Passive Fire Protection” by Jenna Aker
Firestop Contractors International Association (FCIA) 2018 Webinar Series “M is for Maintenance & Barrier Management Systems” by Bill McHugh, FCIA
Adhesives.com blog post “A History of Firestop in the Building & Construction Industry” by Sharron Halpert, Halpert Life Safety Consulting owner
"Deadliest American Disasters and Large-Loss-of-Life Events" by Lorna Jarrett Blanchard
Firehouse “Lesson’s from the past: MGM Grand Fire” by Azarang (Ozzie) Mirkhah
Chamberlin Quarterly Newsletter
Subscribe Today!
Stay-in-the-know and subscribe to our blog today!