Air Infiltration and Water Penetration Testing of Glazing Systems
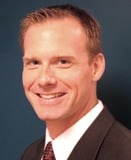
By: Richard J. “Jeff” Gish, P.E. Senior Associate, Terracon Consultants, Inc.
In recent years, the waterproofing consulting industry has witnessed an increasing demand for air infiltration and water penetration testing of the building envelope and glazing systems. This article will focus on field testing of installed fenestrations, storefront and curtain walls systems, and sloped glazing systems. Testing is generally done to document performance of buildings that are under construction or being renovated, but it can also be performed on existing buildings, in a diagnostic or forensic capacity, to identify improper installation, inadequate performance or material defects in the installed systems. As of late, several factors have combined to create an increased demand for testing services:
- Testing requirements are now included in most specifications and are generally required as a means of quality assurance during construction to document that the assemblies (and their integration into the barrier system) are performing to the appropriate specifications.
- Glazing systems are constantly evolving leading to new technologies and building techniques that make them increasingly air and watertight.
- Increased focus on green building (LEED®, energy efficiency, carbon footprint) demands that the systems perform to higher standards and under tighter tolerances than their predecessors.
- The public has become aware of the potential negative impact of water infiltration on building materials (mold, reduced indoor air quality, structural decay).
- Energy costs are expected to increase in the future. Leaky, inefficient systems increase a building’s operating cost making owners and property managers more focused on constructing (and documenting) an air and watertight building envelope.
- In some cases, deficiencies in the design and/or installation of glazing systems result in significant damage and costly insurance claims or litigation. In these cases the source, origin and pathways of the water infiltration must be documented in order to determine the cause(s) of damage and the responsible parties.
The test methods in common use today are somewhat interrelated and are published by two organizations: American Society for Testing and Materials (ASTM) International and the American Architectural Manufacturers Association (AAMA). These organizations reference laboratory tests (to establish design performance) and field tests (to document installed performance). Some AAMA documents reference ASTM test methods but with a slightly different procedure or with additional requirements. The test procedures are also relatively new. These factors can combine to create some degree of confusion for the owners, architects, design professionals and contractors involved in the project.
Not surprisingly, the first challenge that testing consultants often face is getting everyone involved in the project “on the same page” from a testing perspective. The testing consultant will review the available specifications, drawings, submittals and manufacturer’s literature in order to identify the type, frequency, number and schedule of tests, and the test pressures and allowable leakage rates for the products to be tested. Some specifications are very well written and provide all of the above data with no ambiguity. However, many specifications are ambiguous, insufficient in scope, poorly written or absent of the data required for testing. Some of the common challenges the testing consultant faces when developing a testing proposal include:
- The designated test pressures and/or allowable air leakage rates are not in agreement between the laboratory tests (performed before the project started, usually for the manufacturer) and the field tests to be performed after installation.
- The designated test pressures and/or allowable air leakage volumes for field testing are not consistent with the manufacturer’s published data.
- The project documents contain no direction as to the method of specimen selection and/or the minimum size of each test specimen.
- The project documents contain no direction as to the testing schedule (stage of installation at which to test – all tests at the end of the installation, test at 10%, 35% and 70% completion, test the first 30 linear feet of system installed, etc.) or the number of specimens to test for each test event.
- The percentage of the area to be tested is not consistent with accepted standards. On a recent small curtain wall retrofit project the architect used a testing specification from a previous large office building. As a result, the specifications required that the consultant test nearly 90% of the total installed curtain wall.
FIELD ACTIVITIES
Once armed with a detailed and appropriate scope of testing, the consultant employs a variety of technology and equipment to perform air infiltration and water penetration testing. These test procedures range from use of a calibrated hand-held spray nozzle (AAMA 501.2) to large-scale testing using a vacuum chamber assembly and calibrated spray rack to simulate a wind-driven rain on a building under cyclic pressure (common tests include ASTM E783, ASTM E1105, AAMA 502 and 503).
The vacuum assemblies, instrumentation, spray racks and wands used in these test procedures are typically commercial systems that have been custom-manufactured specifically for testing. However, some consultants use “pieced-together” or “home-built” systems made from parts available at your local home improvement store. Regardless of the type or manufacturer of the test equipment, ASTM and AAMA require calibration of the equipment at six month intervals.
Hand-Held Testing
Prior to testing, the consultant will perform a visual observation of the test specimens and document any notable features or defects in the specimen. For a hand-held spray test (AAMA 501.2), the exterior of the specimen is sprayed with water at a given pressure and volume, and the interior of the specimen is visually observed for water infiltration. Generally speaking, if water leakage occurs, the specimen fails the test, at which point the consultant may confer with the installation contractor and project team to determine possible causes of failure and appropriate corrective actions.
Chamber Testing
In the more stringent chamber tests, pressure chambers are fitted to the interior or exterior face of the test specimen to develop a pressure differential across the specimen. The consultant will create a negative pressure differential on the interior of the specimen and document the air infiltration rate through the test specimen. If the actual rate is higher than the allowable rate, the specimen fails the test and corrective action is required.
Water penetration testing is performed after the air test; in some cases air infiltration testing is not specified so the water test is the only test required. Pressure chambers are fitted to the interior or exterior face of the building envelope aroundthe test specimen as opposed to being fitted directly to the specimen in the air test. A water spray rack consisting of a grid of calibrated spray nozzles is fitted to the exterior of the test specimen to simulate a rain event. The consultant will create a negative static or cyclic pressure differential on the interior of the specimen and document any water penetration beyond the inside edge of the test specimen. If water penetrates beyond the innermost face of the test specimen, the specimen fails the test and corrective action is required.
Chamber testing can also be used in forensic investigations of existing buildings, such as is outlined in ASTM E2128 and AAMA 511. In some cases, the appropriate test pressures may be provided by the manufacturer. Alternatively, the consultant may research the historical weather data and determine wind speed and direction at the time the specimen failed and calculate (via ASCE 7) the pressure on the specimen at the time of failure. The consultant will use that pressure as his basis for testing with the approval of the Architect/Engineer of Record.
CONCLUSION
Who will benefit from air infiltration and water penetration tests? Everyone. Architects, engineers and contractors will have written documentation that the field installed systems are performing to manufacturer’s specifications. Building owners can expect lower energy costs and an increased service life of building systems. Building occupants and tenants are more comfortable due to reduced temperature fluctuations. The risk of future moisture related material damage and biological growth is reduced. In cases where existing systems are not performing adequately, testing by a skilled consultant will identify how, why and where the systems are failing so that the appropriate corrective actions can be taken.
Mr. Gish joined Terracon Consultants, Inc. in 2005 and is a Senior Associate. Mr. Gish is Terracon’s Practice Leader for building envelope testing and infrared thermography and manages the Facilities Services groups of several of Terracon’s Texas offices. His primary focus is the forensic assessment of failed or deficient building systems and components. He can be reached at 210.641.2112 or via email
Subscribe Today!
Stay-in-the-know and subscribe to our blog today!